Overview
This topic covers:
This document shows how to prepare asset management plans, and to ensure the plans will pass the scrutiny of:
- Regulators
- Government stakeholders
- Customers
- Shareholders (if applicable).
It is important that the plans be prepared in a structured way, to ensure that valid conclusions have been reached, and a clear direction and strategy is presented for future service delivery.
Asset owners and managers are making decisions on best practice applications for their asset groups. These practices are being tied to world's best practice, however not every asset or business requires world's best practice asset management.
Organizations are producing guidelines, however the key is to successfully adapt them to suit the individual asset needs.
KEY BUSINESS DRIVERS | OUTCOMES NECESSARY | BUSINESS ENVIRONMENT WEIGHTING |
Improved Operational Efficiency & Effectiveness | Optimized Maintenance System Modeling Automation Cost Minimization Current Utilization Available Capital | 60% |
Improved Levels of Customer Service | System Performance Satisfied Customer Satisfied Regulator | 20% |
Achieve Optimum Life from Existing Assets | Deferred Capital Optimal Blend of Capital and Maintenance | 20% |
Organizations must be able to answer the key asset management questions, which are:
- What are the assets of the organization?
- What do they consist of (their physical details)?
- Their present replacement and written down value?
- The condition they are in and at what rate are they being consumed (decay)?
- What standard of service is required from them?
- How are they likely to fail to meet service standards?
- What will be the impact of these failures on the service delivery?
- The optimal strategy to counter these failures?
- The optimal maintenance required to provide the necessary reliability or cost effective life within the business framework?
- Whether or not they should be rehabilitated or replaced and when this should take place?
- The cost of operations and these future maintenance, rehabilitation and replacement programs?
- How can these programs be financed, and the impact on customers and stakeholders?
- How would different levels of funding affect the level of service?
The key change for asset owners is to shift from the practice of looking at things historically, to knowing exactly what is going on right now (the present) and having an accurate picture of what is likely to happen in the future.
To do this, organizations need to develop a total asset management plan, through which the business can gain a clear picture of probable scenarios that will impact on their business activities.
It is vital to develop a plan that suits the business and this needs to be done by looking at the benefits/costs of undertaking this activity.
The costs associated with developing a total asset management plan are quite significant and for those organizations with a large portfolio of assets the way in which they tackle these projects will have a significant impact on the resources required.
The key cost drivers are the components that make up the plan:
Asset register
The detail of the asset register is dependent on the hierarchical level down to which data is collected. In asset management terms this is known as the Maintenance Managed Item (MMI). It is the level at which work orders are raised or maintenance carried out
Condition and performance of asset
The level of sophistication of condition assessments and performance monitoring
Predictive modeling
The modeling of the different failure modes by which the assets are likely to fail to meet their service standards.
Risk exposure
The analysis and assessment of the probability and consequences of the predicted failure modes. It is assessed in economic cost to the organization - direct and indirect costs.
Optimized renewal strategy
The identification of the most appropriate renewal strategy for the organization. It involves a blend of recurrent and capital expenditure in the form of maintenance, operation, rehabilitation, replacement and non-asset (for example: demand management) activities.
Optimized maintenance
Within this optimized renewal strategy, the organization will need to complete the optimal day-to-day operations and maintenance activities.
The key activities are the analysis of optimized renewal programs and detailed maintenance analysis to match this.
To be able to complete these activities we need data or inputs from:
- Maintenance histories, activities and costs in both direct and indirect terms
- Operational cost, breakdown
- Standards or qualities of service
- Current risk exposure assessments.
In completing the Optimized Renewal Decision Making analysis (ORDM) we will need to identify benefits such as:
- Likely maintenance cost reductions
- Likely operational cost reductions
- Improved level of service or reliability of asset
- Increased value of asset
- Potential to increase income due to more reliable and efficient service
- Risk reduction opportunities including:
- Reduced business risk exposure (direct)
- Reduced impact on customers (indirect).
To be able to decide on the level of sophistication of the TAMP we need to have a reasonable assessment of its cost and benefits.
By completing a simple needs analysis and rating the costs and benefits by either a point score or nominal economic value method, the organization should be able to decide on the degree of sophistication that is warranted for the asset management plan.
To ensure this work is carried out successfully there are two key success factors, and these are:
- The commitment by the organization for the need to improve our asset management and develop TAMP of appropriate sophistication
- The identification of an achievable program and appropriate timeframe with key deliverables.
The organization needs to set tangible planning targets by which they can meet the needs of the business and the assets in a cost effective manner.
The following figure shows how this can be achieved, by targeting appropriate improvements in different areas over an acceptable timeframe.
It shouldn't happen overnight but can be programmed to evolve over 5 years, appropriately rationalizing available resources to achieve a satisfactory quality.
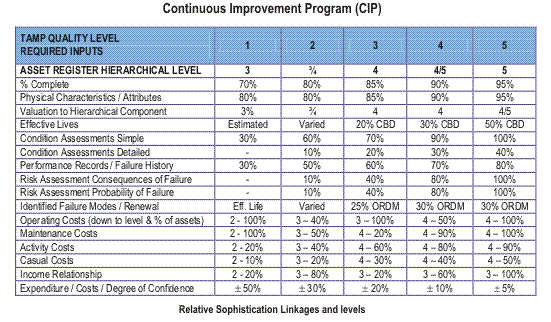
The key elements of any improvement strategy involves the following activities:
Initial risk assessment
By adopting a simple risk assessment technique all facilities or system elements can be ranked according to which pose the greatest business risk to the organization. This can be done by applying nominal values to the various consequences of failure for the system elements. The probability of failure can be estimated based on organizational knowledge, experience and the evidence of failure histories.
Secondary risk assessment
The secondary assessment should focus on those elements or components of the system that represent the greatest risk to the organization. By using a more sophisticated risk assessment process, the asset management teams are then able to rank the individual facilities, assets or their components in terms of their current business risk exposure.
Detailed renewal strategies
A detailed study program can now identify all the key tasks for renewal. The effort required to complete this can be judged against the potential risks and benefits to the business.
Once this TAMP workload has been identified, the activities can be resourced using a blend of in-house staff, experts and consultants as required.
Once this assessment is complete the asset management improvement strategy can be matched to the level of sophistication or quality of the TAMP.
The individual activities that make up the asset management improvement strategy can then be prioritized to suit the greatest benefit/costs to the organization with the whole approach delivering an increasing quality of total asset management plans over an acceptable timeframe.
An example of this approach is shown below.
Each organization needs to develop this type of plan for each key asset system to ensure they are committing their resources and efforts to best suit their business needs or risks.
Improvement Program Progress – Improved Sophistication Level of Confidence
| TAMP Version |
SYSTEM | 1 | 2 | 3 | 4 | 5 |
Degree of Confidence | ± 50% | ± 30% | ± 20% | ± 10% | ± 5% |
Hierarchical Level | 3 | 3/4 | 4 | 4/5 | 5 |
Asset Registers |
Hierarchical Levels Completed | 100 | 100 | 100 | 100 | 100 |
Priority: | . | . | . | . | . |
. | Physical Attributes | 40 | 60 | 80 | 90 | 100 |
. | Economics (Valuations) | 60 | 70 | 80 | 90 | 100 |
. | Other Details (Model No. etc) | 30 | 50 | 70 | 80 | 90 |
Asset Accounting/Costing |
Historical | 100 | 100 | 100 | 100 | 100 |
Current Cost/Accrual | 25 | 50 | 100 | 100 | 100 |
MEERA Values | 0 | 50 | 100 | 100 | 100 |
Optimized Values | 0 | 50 | 100 | 100 | 100 |
Straight Line Depreciation | 100 | 100 | 100 | 100 | 100 |
Renewal Annuity | 0 | 50 | 100 | 100 | 100 |
Maintenance System Data |
Procedures | 40 | 50 | 90 | 100 | 100 |
Schedules | 60 | 70 | 90 | 100 | 100 |
Materials/Labor Resources | 0 | 10 | 30 | 50 | 70 |
FMECA Tools | 0 | 20 | 40 | 50 | 60 |
Condition Assessment |
Effective Lives: (LTD) | . | . | . | . | . |
.. | Estimated | 100 | 100 | 80 | 70 | 50 |
. | Condition Based | . | . | 20 | 30 | 50 |
Basic 1 - 5 | 100 | 75 | 25 | 0 | 0 |
Medium 4.5 - 5.9 | . | 20 | 50 | 65 | 60 |
Sophisticated 1 - 1 000 | . | 5 | 25 | 35 | 40 |
Performance Monitoring |
Asset Failures (outages) | 75 | 100 | 100 | 100 | 100 |
Quality Failures: | . | . | . | . | . |
. | Basic | 20 | 50 | 100 | 100 | 100 |
. | Sophisticated | 0 | 25 | 50 | 75 | 100 |
Quantity Failures | 75 | 100 | 100 | 100 | 100 |
Reliability / Response | 25 | 50 | 100 | 100 | 100 |
Predictive Models/Failure |
Capacity/Demand: (Network) | . | . | . | . | . |
. | Utilization | 0 | 10 | 20 | 30 | 40 |
Reliability - MMS | 0 | 5 | 20 | 35 | 50 |
Mortality - Decay Models | 0 | 0 | 20 | 40 | 60 |
Cost - Financial | 10 | 20 | 35 | 50 | 60 |
Probability of Failure: | . | .. | . | . | . |
.. | Simple (Interview) | 90 | 70 | 45 | 25 | 0 |
. | History MTBF (Non Critical) | 10 | 20 | 35 | 45 | 60 |
. | Predicted PF y=dxn | 0 | 10 | 20 | 30 | 40 |
Risk Assessment |
Consequence of Failure: (Critical) | . | . | . | . | . |
. | Simple | 50 | 90 | 70 | 40 | 0 |
. | Medium Risk | 0 | 10 | 20 | 30 | 30 |
. | Sophisticated Models | 0 | 0 | 10 | 20 | 50 |
. | Automated | 0 | 0 | 0 | 10 | 20 |
Consequence of Failure: (Non Critical) | . | . | . | . | . |
. | Simple | 20 | 40 | 50 | 10 | 0 |
. | Medium MMS | 0 | 10 | 40 | 50 | 40 |
. | Economic | 0 | 0 | 10 | 30 | 40 |
. | Automated | 0 | 0 | 0 | 10 | 20 |
Risk Cost (exposure) | . | . | . | . | . |
. | PF x CF x Redundancy | 20 | 50 | 70 | 80 | 100 |
Optimized Renewal Decision Making |
Renewal Treat Options Benefits | 60 | 70 | 80 | 90 | 100 |
Extension of Life (Simple Decay) | 3 | 40 | 50 | 60 | 70 |
Reduction Operations | 0 | 10 | 30 | 40 | 50 |
Reduction Maintenance | 0 | 10 | 30 | 40 | 50 |
Improved Production | 0 | 0 | 10 | 20 | 30 |
Levels of Service | 0 | 0 | 10 | 30 | 50 |
Risk Reductions | 0 | 10 | 25 | 40 | 50 |
Asset Creation |
Simple | 0 | 95 | 85 | 80 | 60 |
Complex (ORDM) | 0 | 5 | 15 | 20 | 40 |
Budget Rationalization |
Simple | 50 | 60 | 60 | 30 | 0 |
Medium | 10 | 40 | 30 | 50 | 70 |
Complex | 0 | 0 | 10 | 20 | 30 |
Operations |
Manual/Experience | 100 | 90 | 60 | 40 | 20 |
Semi Automated (PLC) | 0 | 10 | 30 | 40 | 30 |
RCM/SCADA | 0 | 0 | 10 | 20 | 30 |
Expert Systems | 0 | 0 | 0 | 10 | 20 |
Costing to Hierarchical Level | 50 | 100 | 50 | 4/100 | 4/100 |
Maintenance Practice |
Resource Driven | 40 | 40 | 50 | 60 | 70 |
Reactive | 60 | 70 | 50 | 40 | 30 |
Planned: | . | . | . | . | . |
. | Historic | 40 | 50 | 50 | 10 | 10 |
. | FMECA/RCM | 0 | 0 | 20 | 30 | 30 |
. | Economic | 0 | 0 | 10 | 20 | 30 |
Spares Optimization | 20 | 30 | 40 | 40 | 50 |
Costing to MMI | 50 | 80 | 100 | 80 | 100 |
Resource / Work Management |
Simple | 100 | 90 | 60 | 40 | 20 |
Medium | 0 | 10 | 30 | 40 | 50 |
Complex | 0 | 0 | 10 | 20 | 30 |
Legend 10 = Percentage of all assets in register in which practice is complete. |