Life Cycle Costs
This topic covers:
Life cycle costs are:
The costs associated with acquiring, using, caring for, and disposing of physical assets including feasibility studies, research, design, development, production, maintenance, replacement, disposal, support and training, and operating costs of the asset.
Every maintenance action performed on an item incurs some cost, in the form of staffing or materials. In many cases, this cost is offset by a benefit of equal or greater imputed value, in the form of enhanced equipment reliability/plant availability. However, in many other cases, a maintenance action could not provide any net benefit and would waste resources.
The cost of providing maintenance is:
TOTAL COST = DIRECT COSTS + INDIRECT COSTS
Where DIRECT COSTS = Labor, materials and overheads
and INDIRECT COSTS = Lost production and environmental damage
The direct costs of maintenance are normally preventive and corrective maintenance costs. The blend of these to provide a minimum total cost is the primary aim once the indirect costs have been considered.
Despite its significance, cost is normally the last criterion to be considered in determining maintenance policy, since it only becomes relevant after one or more potentially effective tasks or processes have been identified. When an effective task or process has been identified, and in the absence of binding constraints such as the need to perform a task for the purposes of establishing or maintaining capability, some form of benefit versus cost analysis provides the means of determining the relative efficiency of different maintenance alternatives. Studies have shown that 70% of expenditure is consumed by operations and maintenance activities.
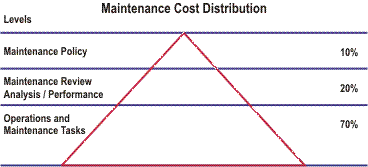
Cost benefit analysis may be performed at different levels depending upon the level of information available and the complexity of the problem. In each case, the objective of the analysis may be stated theoretically as "to select the least cost alternative which satisfies the maintenance objective", however, in practice the decision is made more complex by:
- The need to apply the criterion over a wide range of decisions that in many cases involve alternatives that cannot be accurately costed
- Changing circumstances which may render a decision that is cost- effective in the short term, ineffective in the long term
- The difficulty in identifying and computing the full range of costs which have an impact on total cost.
In general, life cycle costs can be estimated by using the following formula:
LCC = Capital Cost (C) + Lifetime Operating Costs (O)
+ Lifetime Maintenance Costs (M)
+ Lifetime Plant Losses (L)
+ Plant Disposal Cost (D)
The values used for estimating LCC must be adjusted for variations in the dollar value with time by using a discounted cash flow and applying the following criteria to the formula:
- Define the boundary of the analysis
- Establish the life cycle cost structure
- Determine the appropriate estimating technique
- Determine the probable life of the asset
- Estimate costs in present day prices
- Estimate inflation rates
- Determine the net present value of each cost element.
EXAMPLE
A machine incurs operating costs of $4 000 the first year and it is expected these costs will increase $500 each year thereafter for the 10 year life of the machine. If money is worth 15% per year, what is the equivalent annual worth of the operating costs?
Maintenance can have a dramatic impact on life cycle costs via the impact of the indirect cost of downtime and unavailability. It is important that maintenance policy is accurately determined to minimize life cycle costs.