Technical Factors Affecting Asset Lives
This section discusses the technical factors that should be considered when determining asset standard economic lives.
In general, the technical life of an asset is a function of the assets’ physical characteristic, the organization approach to asset management, and the physical environment within which the asset is operated.
The physical condition of any asset depends on a number of factors:
- Design standards
- Construction quality
- Material quality
- Operational stresses
- Maintenance history/ Practice
- Asset working environment
- External Stresses
Where a organization has the knowledge and experience with the assets and relevant technical factors, it will be able to establish a matrix of technical lives for assets constructed during different periods of time, at different locations, and operating under different conditions. The quality of the information will determine the validity of such matrices.
Design Standards
In some situations the original specification or design of an asset contains a basic flaw. The performance of the asset could be severely restricted due to this fault. By assessing historical maintenance records and interviewing key maintenance and operation personnel with a long knowledge of the asset system, it is possible to identify assets that are being affected by such faults and correct their technical lives accordingly.
Construction Quality
This element relates to the quality of workmanship used in the construction of an asset. In many cases the specification and materials may prove to be perfect but ineffective on-site supervision of construction techniques or faulty workmanship may result in a significant reduction in technical lives.
In some cases this issue can be isolated to a certain contractor, a construction team, a work supervisor, or even to a period in time where the works constructed were not to an appropriate standard of workmanship for that type of asset. As a result the technical lives could be significantly reduced for the assets affected.
Material Quality
As with the construction quality, it is often the case that materials that have tested perfectly at acceptance will have some basic fault that may shorten the lives of the assets. In some cases this may reflect on a minor component such as a rubber ring in a joint. In other cases it may involve the parent material, for example the casting or the extrusion of pipes.
Investigation into material quality impact can be assessed by reviewing failure histories and issues associated with this element.
Due to advancement in technology, it is also generally expected that the technical life of an asset constructed in the earlier period of development will not be as long as a similar asset constructed in a later period. For example, cast iron mains constructed in the 1920’s may have a shorter technical life than cast iron mains constructed in the 1970’s.
Operational Stresses
In some cases assets have been operated outside the normal working conditions for which they have been designed. In this case the additional stresses generated may result in the reduction in technical lives of the assets.
Maintenance History/Practice
In many cases assets that have been properly constructed using appropriate design standards and material specifications behave perfectly in the early years of life. However, inappropriate or inadequate maintenance may then have been carried out over an extended period due to budget restraints or ignorance. This can have a considerable effect on the technical lives of such assets.
In most cases this has a major impact on mechanical and electrical devices. However, in some cases, inappropriate maintenance on large passive (civil) assets can also have a considerable impact, for example, failure to maintain cathodic protection systems for steel main pipe systems.
Asset Working Environment
In most cases the key factor that affects the technical life of an asset involves its working environment. For those assets located underground, aggressive ground conditions or ground movement can have a significant impact. Corrosion of metal piping can significantly reduce the expected technical life. For those assets that are located above ground, their exposure to sun, wind, and moisture, or even light, can have a significant impact on technical life.
It is essential to review all available information through maintenance records and the knowledge and experience of staff to derive an outline of the areas in which these conditions will have an affect on the lives of the assets. Assessments can be made as to the overall impact and the technical lives corrected accordingly.
External Stresses
In some cases asset lives will be affected by the fact that they have been exposed to considerable external stress. These include:
- Ground movement
- Geological pressures
- The pressure of road transport or other structures against underground pipe work, etc
In the case of pipe materials, the time to rupture is dependent on the magnitude of the stresses exerted on the wall of the pipe. The higher the stresses, the shorter the time to rupture. The stresses exerted on the wall of a buried pipe are typically earth loads, pavement loads and vehicle loads, as well as incidence of ground movement. In the case of polyethylene (PE) pipes, the effect of ground temperature may also have an impact on the technical life of the pipes.
Distribution of Technical Life
It is evident from field experience that like passive assets may fail differently and that failure distribution will most likely follow the Weibull distribution. This means that similar assets constructed or installed at the same time may require replacements at different times because of different product quality controls or different operating conditions. For example, for a polyethylene main with a nominal life of 60 years, 15% of the assets may fail within 50 years, 70% of the assets may fail within 55 to 65 years, and the remaining 15% of the assets may have lives longer than the average of 65 years. The following diagram illustrates the Weibull effect.
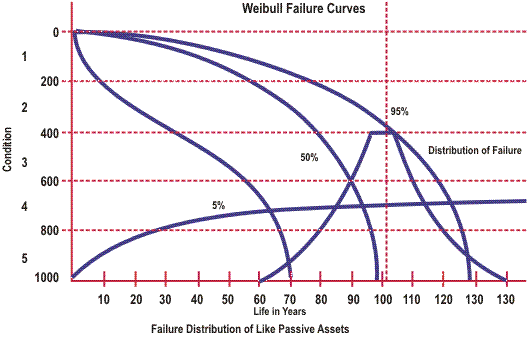
A technical life distribution for each group of assets should be established through a workshop with the operational, maintenance, and engineering staff who have direct involvement with the assets concerned. The staff should first be asked to nominate the base (nominal) technical life of the asset. As a starting point, the life suggested by the manufacturer may be accepted as the nominal life. The staff should then suggest the likely distribution of possible lives for the same asset operating under average conditions based on their experience of earliest failure and latest failure of the same asset. The weighted average of the distributed life is then calculated and adopted as the initial technical life of the asset.
This process is illustrated by an example for pipes:
. | PE | PVC | Steel Coated |
Nominal Life | 60 | 60 | 100 |
Life Distribution | Percentage Distribution |
30 | . | . | . |
40 | 5 | 5 | . |
50 | 15 | 40 | . |
60 | 60 | 40 | . |
70 | 20 | 10 | . |
80 | . | 5 | 15 |
90 | . | . | 15 |
100 | . | . | 60 |
110 | . | . | 10 |
120 | . | . | . |
130 | . | . | . |
Weighted Average | 59.5 | 57.0 | 96.5 |
The weighted average life is rounded and adopted as the initial technical life expected under minimum satisfactory design and operational standards requirements.
Adjustments for Technical Factors
To adjust the initial technical life of the asset it should be rated, for example from 1 to 5, based on some adopted definitions for each of the factors affecting technical life such as:
Factors | Ratings |
. | 1 | 2 | 3 | 4 | 5 |
1. Design Standards | Excellent or high standards used | Good design standards used | Average design standards (50%) | Only nominal standards followed | None or very little design completed (ramshackle) |
2. Construction Quality | Excellent quality and supervision | Good quality and supervision | Average workmanship. Some QA | Poor quality workmanship and QA | Very poor workmanship and no QA |
3. Material Quality | Excellent materials used | Very good materials used | Average materials used | Poor quality materials used | Inappropriate materials used |
4. Operational Stresses | Asset operated below working specifications | Asset sometimes over-loaded | Average over-loading experienced | Asset regularly over-loaded | Asset extensively overstressed |
5. Maintenance History/Practice | Well or over maintained | Reasonable maintenance | Average maintenance | Poor maintenance practice for most of life | Never maintained over life |
6. Asset Working Environment | Very good environment (stable) | Good operating environment | Below average environment | Humid, salty, some movement | Freezing, humid, aggressive atmosphere, or geology |
7. External Stresses | No external stresses | Only minor external stresses | Above average external stresses | High external stresses experienced | Severe external stresses have been experienced |
The ratings are related to the likely impacts on the technical lives of the assets in terms of the percentage variance on the lives of the assets according to past experience as well as cognitive judgment. It is critical that the ratings-impacts relationship be established through a consultative process with the expert groups within the organization.
The significance of the different factors is also demonstrated by the extent of variance on the technical lives. For instance, good design standards rated as 1 may have a positive 10% impact on the effective life, whereas good construction quality rated as 1 may have a far more significant impact of positive 25% on the technical life.
The following example shows typical impacts (variances) on underground pipeline asset technical lives as a result of different factors. These are applicable to all network assets.
Note that it is not appropriate to add up all of the variances to derive the total adjustments required since some of the factors may be influenced by others. For example, the presence of adverse ground condition (operating environment) may be well compensated by good design or construction quality.
A suggested industry practice is to adopt the impact from the worst contributing factor and to add or subtract 30% of the remaining impacts, with a limiting adjustment on the effective life of +50% or -40%.
This example illustrates the adjustments from the above process:
. | PE | Steel |
Impact Factors | Ratings | Variance | Ratings | Variance |
1. Design standard | 1 to 2 | +7.5% | 1 to 2 | +7.5% |
2. Construction quality | 3 | -12% | 1 to 2 | +15% |
3. Material quality | 1 | +10% | 1 | +10% |
4. Operational stresses | 1 to 2 | +10% | 1 to 2 | +10% |
5. Maintenance history | 3 | -5% | 2 to 3 | +2% |
6. Operating environment | 1 | 0% | 2 | -10% |
7. External stresses | 1 | 0% | 2 | -5% |
Total Adjustments | . | -7.5% | . | -2.1% |
. | . | . | . | . |
Average Life | . | 60 | . | 96 |
Adjusted Life | . | 55 | . | 95 |
In the above example, the worst contributing factor for PE mains is the poor construction quality, which has a negative impact of 12% on the technical life of the main. The other impacts have a total variance of +22.5%; 20% of the latter is added to the worst contributing impact with the total adjustment of minus 7.5%.
The adjusted technical life of the PE main after taking the above factors into consideration is, therefore, 55 years.
|
previous |
home
|
next |
ODV Principles and Methodology for Determining Asset Lives |
|
Economic Life Factors
|
|